The conveyor system consists of multiple moving parts and components, including conveyor belts, rollers, winches, bearings, couplings, reducers, motors, fluid couplings, and scrapers. The main function of the entire system is to move materials from point A to point B. While each component has its unique function, the conveyor belt is undoubtedly one of the most important and often overlooked parts of the conveyor system.
■ What is a Conveyor Belt?
The conveyor belt is one of the most crucial components of the conveyor system, responsible for transporting bulk materials from the site to processing facilities or loading areas. Conveyor belts are typically driven by electric motors and are spliced and vulcanized according to actual needs. Traditional conveyor belts are composed of three layers: the top or cover layer is used for transporting products, the middle layer (also known as the carcass) provides support, usually made of metal or woven fabric, and the bottom is a cover layer. Depending on the actual application or environment, the composition of conveyor belts may include plastic or rubber compounds, fabric materials, and steel cables.
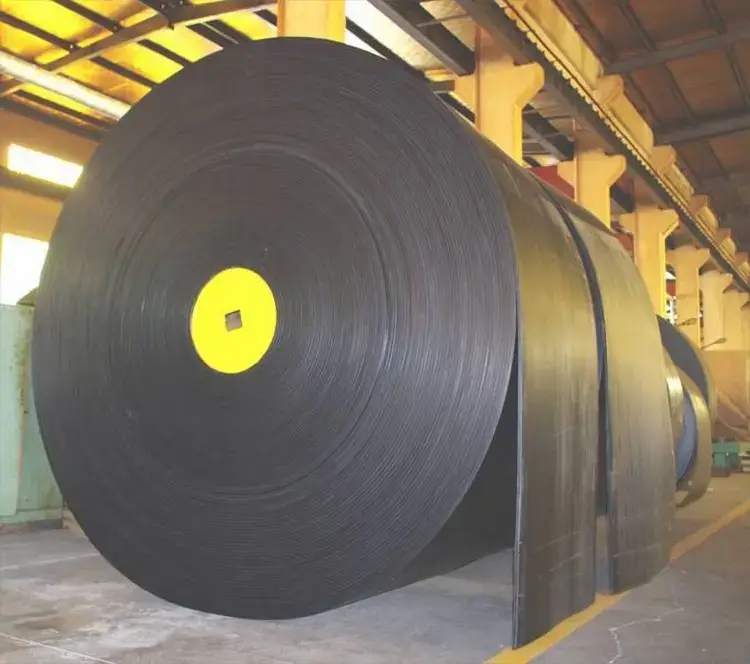
■ Different Types of Conveyor Belts
Conveyor belts are widely used in various industries, and thus there are multiple types to choose from, depending on different factors such as industry, application, and environment. Incorrect use of conveyor belts may lead to project delays and even catastrophic consequences. Therefore, selecting the correct type of conveyor belt is an important consideration for everyone:
1. By structure: standard and impact-resistant types.
2. By purpose: in addition to standard types, there are wear-resistant, heat-resistant, cold-resistant, acid and alkali-resistant, flame-retardant, tear-resistant, ozone-resistant types, etc.
3. By category: based on the performance of the cover rubber, it can be divided into various types such as ordinary steel wire rope conveyor belts, flame-retardant steel wire rope conveyor belts, heat-resistant steel wire rope conveyor belts, wear-resistant steel wire rope conveyor belts, cold-resistant steel wire rope conveyor belts, acid and alkali-resistant steel wire rope conveyor belts, oil-resistant steel wire rope conveyor belts, and flame-retardant steel wire rope conveyor belts. These types have higher strength than ordinary conveyor belts, longer lengths, and can reduce transfer points, saving energy and management costs.
■ EP Conveyor Belt Specifications
Fabric structure | Fabric specs | Ply thickness (mm/p) | Stiength series (N/mm) | Cover thickness(mm) | Width(mm) | Length(m) |
Warp | weft | 2Ply | 3Ply | 4Ply | 5Ply | 6Ply | Upper | Lower |
Polyester(EP) | Polyamine(P) | EP-80 | 0.6 | 160 | 240 | 320 | 400 | 480 | 1.5-12 | 0-4.5 | 400-2500 | ≤300 |
EP-100 | 0.75 | 200 | 300 | 400 | 500 | 600 | 500-2500 |
EP-150 | 1 | 300 | 450 | 600 | 750 | 900 |
EP-200 | 1.1 | 400 | 600 | 800 | 1000 | 1200 |
EP-250 | 1.25 | 500 | 750 | 1000 | 1250 | 1500 |
EP-300 | 1.35 | 600 | 900 | 1200 | 1500 | 1800 |
EP-350 | 1.45 | - | 1050 | 1400 | 1750 | 2100 | 800-2500 |
EP-400 | 1.55 | - | - | 1600 | 2000 | 2400 |
EP-450 | 1.7 | - | - | 2000 | 2500 | 3000 | 1000-2500 |
■ How to Choose the Right Conveyor Belt
When purchasing mining conveyor belts, first determine the tensile strength requirements, cover thickness, and select the appropriate cover type based on the materials being transported and loaded. The operating environment is equally important, as it directly impacts the choice of conveyor belt.
● When transporting packaging or lightweight materials in temperature-controlled warehouses, steel wire rope conveyor belts can be selected. Steel wire rope conveyor belts consist of core rubber, steel wire ropes, cover layers, and edge rubber. They are resistant to mold, insects, aging, have good heat resistance, and high tear resistance, and can be refurbished after wear. The characteristics of this type of conveyor belt include high tensile strength, good impact resistance, long service life, low elongation, and good flexibility, making them suitable for long-distance, large-span, high-speed material transportation.
● If the conveyor belt operates in an underground environment, it may need to meet MSHA Part 14 fire protection requirements. In this case, it is crucial to choose conveyor belts made from flame-retardant materials. Special agents, impregnating pastes, and rubber components can be added during manufacturing to help reduce the coefficient of friction and increase flame resistance, ensuring operations at the highest safety level.
● On the ground, the choice mainly depends on the characteristics of the raw materials being transported. Factors such as moisture, particle size, and wear characteristics are determinants. For instance, high-wear materials like iron ore, metallurgical coke, and quartz require stronger conveyor belts than moderate-wear materials like ash or sand.
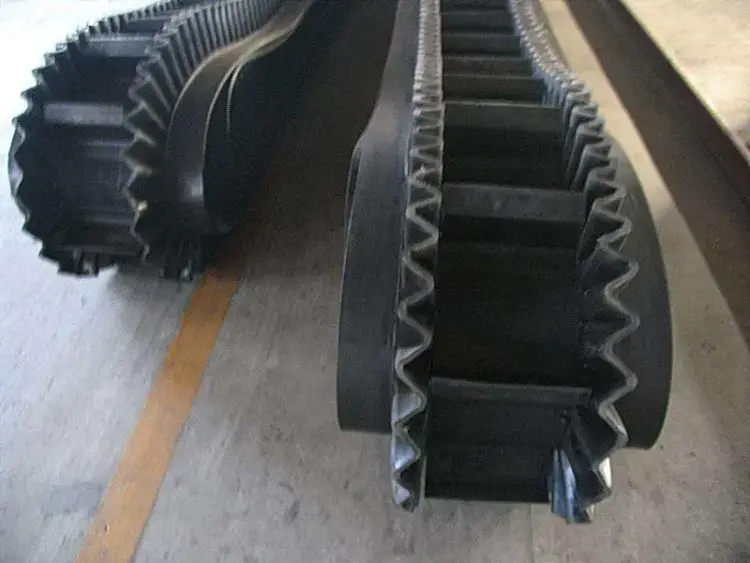
■ Selection Considerations for Other Application Scenarios
● High-hardness items: Under ideal conditions, the average lifespan of a mining conveyor belt is three to ten years, depending on factors such as belt length, conveyor design, and more. The properties of the bulk materials being transported can significantly affect the lifespan of the belt. For example, sharp, serrated, and highly abrasive materials will damage the belt more quickly; thus, selecting a conveyor belt with high tear resistance is most suitable in such environments.
● Corrosive materials: Conveyor belts can corrode due to the presence of metals. While corrosion may not be a significant issue in climate-controlled facilities, it should be prioritized when transporting corrosive items in underground environments or when exposed to factors like temperature fluctuations, UV rays, humidity, and dampness.
● Extreme temperature environments: The temperature of the materials being transported is another important consideration. For example, rocks and ores extracted directly from underground can reach temperatures of up to 220°F. Although this is not high enough to ignite the belt, it can cause irreparable damage. Additionally, when transporting bulk materials from extremely cold environments, the conveyor belt can become very brittle. Therefore, choosing conveyor belts with specific thermal properties or cold resistance based on the actual environment can help mitigate damage caused by extreme environmental factors.
■ Parameters to Understand When Purchasing Conveyor Belts
● Roller diameter: Consider the manufacturer’s recommended roller diameter based on the thickness of the belt from top to bottom.
● Belt width and length: Not all belts are suitable for the same applications, and their widths and lengths may vary accordingly. For example, the width and length of conveyor belts you see at airports are much smaller than those used in underground mines. Although many belts can be customized to the required length and width, it is best to clarify your size requirements when making a selection.
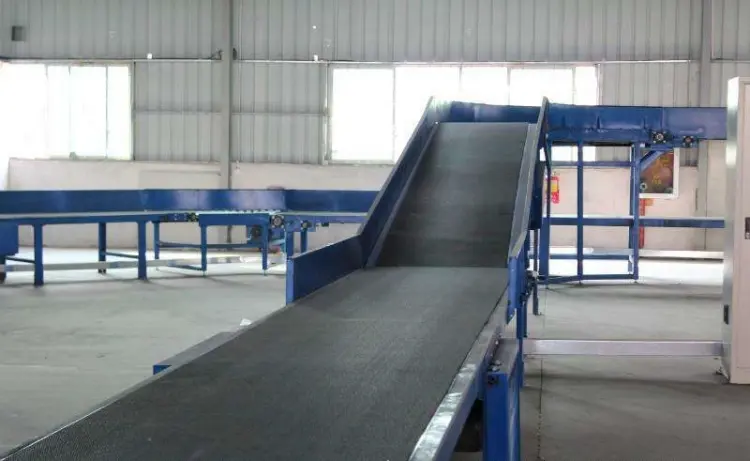
■ Frequently Asked Questions
Q: What is a coal conveyor belt?
A: Coal conveyor belts are specifically designed for the safe and efficient transport of coal from one area to another. Zoomry has over 20 years of experience in manufacturing customized conveyors for the coal mining industry.
Q: What types of mining use conveyor belts?
A: Some examples of mining operations that use conveyor belts include coal, rock, precious metals, iron ore, lead, and lithium.
Q: What is a quarry conveyor belt?
A: Quarry conveyor belts transport materials such as sand, gravel, rocks, marble, or crushed stone from the quarry to their destination.
Q: What does TPH mean in a conveyor?
A: "TPH" stands for "tons per hour," which is a key measurement indicator for determining the ideal conveyor belt used in mining conveyor systems. It measures how many tons of rock or ore the conveyor belt moves per hour. TPH is related to the belt speed or the speed at which the belt moves.