The conveyor drum is a key component in any conveyor system, performing far more than just supporting the conveyor belt. It plays various critical roles, from changing the belt’s direction to driving the belt, controlling its tension, and even protecting the entire system in harsh working conditions. Depending on specific specifications, the drum can serve different roles, including drive drum, head drum, tail drum, tension drum, and snub drum, among others. Zoomry, a leading company in the conveyor systems field, offers high-performance drum products widely used across various industries globally, demonstrating exceptional performance in harsh environments such as sand and gravel quarries, coal mines, unit packaging, food processing, and recycling operations.
In a highly efficient conveyor system, the lifespan of the drum has a critical impact on overall operational costs. A longer drum lifespan can significantly reduce maintenance costs and maximize the system’s production capacity. Thus, the drum's design, manufacturing, and application directly determine its reliability and durability in real-world operations. Zoomry adheres to high production standards to ensure that its drum products can operate stably in extreme conditions, reducing equipment downtime and ensuring continuous production for customers.
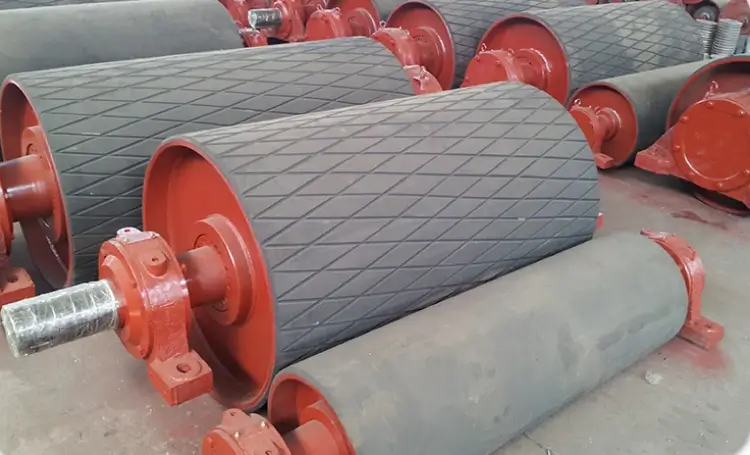
■video
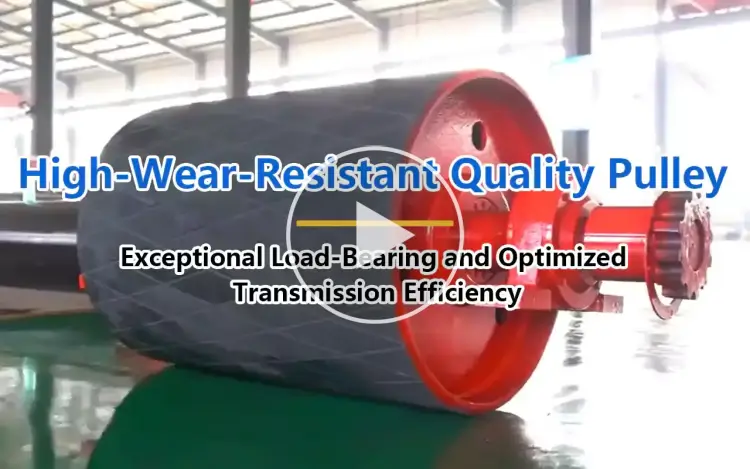
■Applications of Conveyor Drums: Diverse Scenarios and Requirements
1. Electric Drum: Integrated Drive Solution
The electric drum, also known as a motorized pulley, is favored for its compact structure and low maintenance requirements. The design integrates the drive motor into the drum shell, eliminating the need for external drive devices in traditional conveyor systems. Particularly in scenarios where space utilization is critical, such as manufacturing, logistics, and warehousing, electric drums can save equipment space, reduce maintenance, lower energy consumption, and minimize downtime, significantly enhancing the operational efficiency of modern conveyor systems.
2. Drive Drum and Head Drum
The conveyor drive drum, also known as the head drum, is typically located at the front end of the conveyor system and is used to drive the entire system. Powered by motors and gear reducers, drive drums come in various designs, such as flat or crowned, and can be covered with lagging to prevent belt slippage.
The design of the drive drum directly impacts the traction and operational stability of the conveyor belt. Selecting the right drive drum can effectively reduce belt slippage and increase production efficiency. Zoomry’s drive drums perform exceptionally well in sand, coal mining, and other extraction industries, maintaining stable performance even in harsh environments.
3. Return Drum and Tail Drum
The tail drum, also known as the return drum, is typically located at the end of the conveyor system. Its main function is to redirect the conveyor belt back to the drive drum, forming a complete loop. Made of high-strength materials, tail drums can withstand high levels of tension and ensure system stability under heavy loads. Additionally, the return drum helps adjust the tension of the conveyor belt, preventing issues caused by overly loose or tight belts.
4. Idle Drum: Boost Efficiency, Reduce Wear
Idle drums in conveyor systems are responsible for guiding and supporting the conveyor belt. In high-speed systems, high-quality idle drums can effectively reduce belt wear and prevent slippage. Zoomry's idle drums are designed with precision and can operate stably in various industrial environments, extending the lifespan of the conveyor belt.
5. Snub Drum: Enhancing Belt Tension
Snub drums are mainly used to increase belt wrap tension around the drive drum, especially in situations where additional belt traction is required. The application of a snub drum can effectively enhance system stability, reduce belt slippage, and ensure the continuous movement of materials.
6. Take-Up Drum: Flexible Control of Belt Tension
The take-up drum is a crucial component in conveyor systems, primarily used to adjust the slack or tension of the conveyor belt by altering the position of the drum in the frame. It plays a significant role in ensuring smooth system operation, particularly in working conditions where frequent belt tension adjustments are needed.
7. Bend Drum: Handling Complex Conveyor Systems
Bend drums are primarily used at bends in conveyor systems to help the belt maintain proper direction and provide additional tension support. The design and manufacture of bend drums must consider factors such as the belt’s load, speed, and turning radius to ensure smooth operation of the conveyor system.
8. Conveyor Rollers: Product Support and Conveyance
Conveyor rollers are widely used on conveyor machines as supporting components for material transfer. Zoomry’s conveyor roller assemblies are precisely designed to withstand high loads and operate smoothly. In the return section of the conveyor system, rollers also play a supportive role, helping the belt return smoothly.
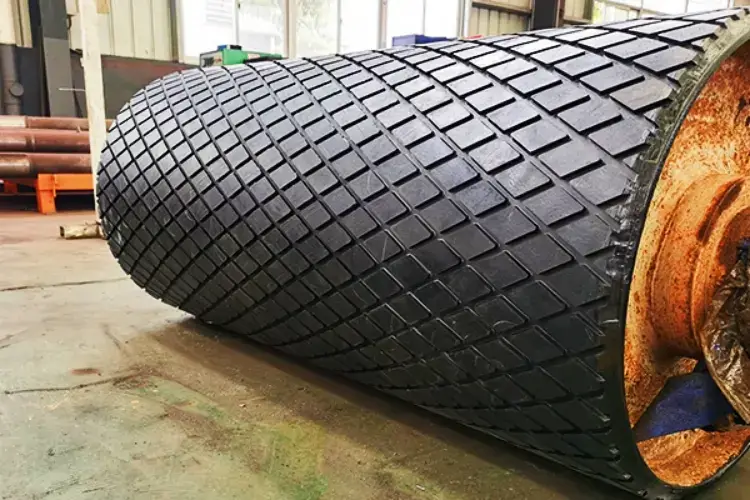
■Specification Table
Diameter of belt roller | 500mm | 650mm | 800mm | 1000mm | 1200mm | 1400mm | 1600mm | 1800mm | 2000mm | 2200mm |
400mm | √ | √ | √ | √ | √ | √ |
|
|
|
|
500mm | √ | √ | √ | √ | √ | √ | √ |
|
|
|
630mm |
| √ | √ | √ | √ | √ | √ |
|
|
|
800mm |
|
| √ | √ | √ | √ | √ | √ |
|
|
1000mm |
|
| √ | √ | √ | √ | √ | √ | √ |
|
1250mm |
|
|
| √ | √ | √ | √ | √ | √ |
|
1400mm |
|
|
| √ | √ | √ | √ | √ | √ |
|
1600mm |
|
|
|
| √ | √ | √ | √ | √ |
|
1800mm |
|
|
|
|
|
| √ | √ | √ | √ |
2000mm |
|
|
|
|
|
| √ | √ | √ | √ |
■Zoomry's Core Advantages
1. Excellence in Welding Technology
Zoomry boasts a team of welding professionals certified under the AWS D1.1 standard, ensuring that the welding quality of each drum product meets international standards. Our welding experts receive rigorous technical training at the company's internal welding training center, ensuring product strength and durability.
2. Rigorous Internal Testing
Before product delivery, Zoomry conducts multiple rounds of stringent internal testing, covering safety, reliability, and cost-effectiveness. Each drum product must pass these rigorous tests to ensure optimal performance in real-world use. We use advanced testing equipment and methods to simulate harsh working conditions, ensuring that our products operate reliably even under extreme circumstances.
3. Custom Drum Solutions
Zoomry not only provides standard products but also offers customized drum solutions tailored to the specific needs of customers. Our technical engineers work closely with clients to deeply understand their application requirements, conduct detailed system analysis, and recommend the most suitable drum type and design. Whether it's motorized pulleys or special-specification drive drums, we can create the most appropriate product for our clients.
4. Extremely Short Delivery Times
Thanks to a global distribution network and efficient production processes, Zoomry can deliver custom products in a very short time. Whether it’s a standard product or a custom drum, we meet client demands while offering fast delivery services. This not only helps clients maintain and replace equipment in a timely manner but also ensures continuous production and reduces downtime.