The long-distance belt conveyor is an intelligent conveying system developed for complex terrains and extended transportation needs, employing modular design principles with single-unit conveying distances up to 20 kilometers and minimum horizontal turning radius of 300 meters. This integrated system combines terrain adaptation technology, dynamic tension compensation systems, and intelligent monitoring modules, replacing traditional multi-stage relay conveying solutions to achieve continuous all-terrain transportation of bulk materials including ores, coal, and aggregates.
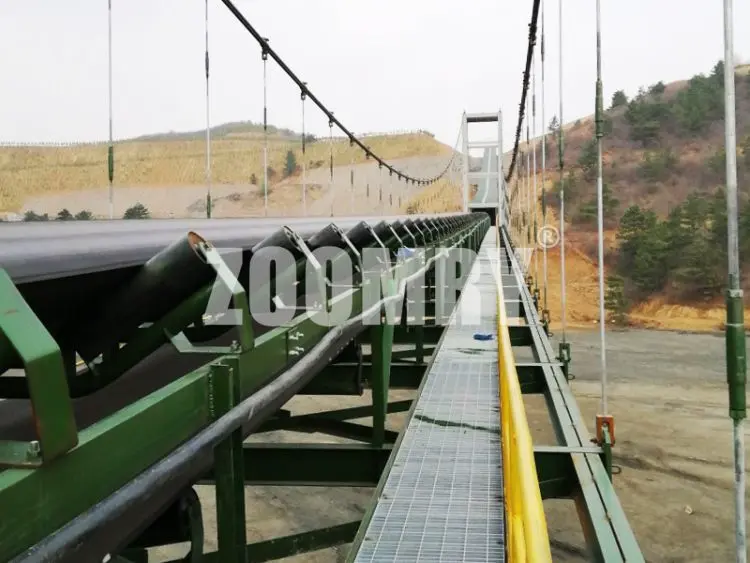
Core Technical Parameters
Category | Parameter Range | Technical Specifications |
---|
Basic Parameters |
|
|
Effective width | 800-2600mm | Customized per material properties |
Unit length | 500m-15km | Terrain-adaptive design |
Belt speed | 0.8-4.0m/s | Variable frequency speed control |
Capacity |
|
|
Max capacity | 12,000t/h | 35°-45° troughing idler angle |
Material size | ≤350mm | Integrated lump breaking system |
Terrain Adaptation |
|
|
Longitudinal slope | -25°~+28° | Anti-slip deep trough structure |
Horizontal turning radius | ≥300m | Dynamic alignment correction |
Component Specifications |
|
|
Drive pulley diameter | Φ630-1800mm | 15-25mm rubber lagging |
Impact idler spacing | 0.3-1.2m | Elastic support damping design |
System Core Advantages
All-Terrain Capability
- 3D route planning: The long-distance belt conveyor utilizes GIS terrain modeling to bypass obstacles like buildings and rivers, minimizing land acquisition
- Dynamic steering system: Hydraulic-assisted steering frames achieve 300m minimum turning radius
- Slope compensation: 28° maximum climbing capacity for mountainous mining terrain
Intelligent Maintenance System (Optional)
- Online monitoring: Integrates 5 sensor types to track 12 real-time parameters including tension, misalignment, and temperature
- Predictive maintenance: Big data analytics predicts bearing remaining lifespan with 3-month advance warnings
- Remote control: SCADA system compatibility for centralized equipment management
Energy-Efficient Design
- Permanent magnet direct drive: 96% transmission efficiency with 25% energy reduction
- Eco-friendly belt: ST-2500 flame-retardant anti-static belt with ≤75dB operation noise
- Solar power option: Photovoltaic storage systems save 300,000kWh annually
System Structure Analysis
Drive Unit
- Dual-drive redundancy maintains 70% capacity during single-point failures
- Hydraulic coupling + inverter coordinated control enables soft start/stop
- IP65-rated permanent magnet motors operate at -30℃~+50℃
Truss System
- Modular 12m truss units with ≤5mm installation tolerance
- Wind resistance: Withstands 10-level wind pressure (0.6kN/m²)
- Anti-corrosion: Hot-dip galvanized for ≥25-year service life
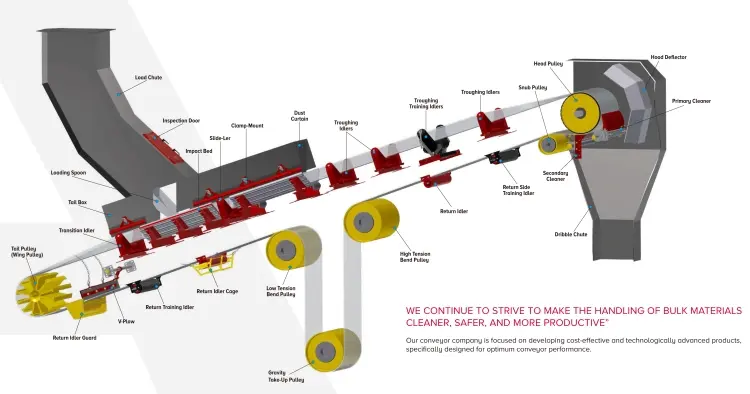
Intelligent Protection Devices
Device Type | Features | Installation Standard |
---|
Bi-directional misalignment switch | 3-stage alarm with auto-correction at 5° offset | Every 30m |
Longitudinal rip detector | Array sensors detect ≥20mm tears | Key transfer points |
Infrared thermometer | Real-time roller temperature monitoring with 70℃ alarm | Drive/return pulley locations |
Typical Applications
Mining Ore Transport
The long-distance belt conveyor enables continuous transportation from open pits to processing plants across complex mountainous terrain. Equipped with steep-angle idlers for 28° slopes and impact-absorbing idlers for ≤350mm lumps. Energy recovery systems in high-drop zones achieve 18%-25% energy savings.
Port Bulk Handling
Fully enclosed chutes with mist dust suppression maintain ≤5mg/m³ dust levels. Hot-dip galvanized + epoxy-coated components withstand ≥15 years of salt spray corrosion. Synchronizes with automated ship loaders for 6000t/h operations.
Aggregate Conveying
Anti-segregation feeders ensure uniform material distribution. Double-layer covers with negative-pressure dust collectors maintain ≤75dB(A) noise. Special anti-adhesion idlers minimize material buildup.
Power Plant Coal Transport
Integrated metal detectors and magnetic separators. Optional electric heating prevents icing in cold climates. Interfaces with digital fuel management systems for real-time calorific monitoring.
Cement Raw Material Transport
12km single-unit long-distance belt conveyors for limestone mines. Wear-resistant ceramic pulleys last 3x longer than standard. Dust-proof chutes with multi-stage airlocks. DCS-compatible for automated control.
Application Comparison
Application | Terrain Adaptability | Environmental Requirements | Maintenance Focus | Smart Needs |
---|
Mining | Complex (Grade A) | Moderate | Impact resistance | Terrain adaptation |
Ports | Flat (Grade B) | Strict | Corrosion protection | Automation |
Aggregates | Rolling (Grade B+) | High | Sealing systems | Measurement precision |
Power Plants | Fixed (Grade C) | Standard | Safety devices | System integration |
Cement | Mixed (Grade A-) | High | Wear parts | Process optimization |
Installation & Maintenance
Field Vulcanization
- Alignment: Laser-guided with ≤2mm deviation
- Step grinding: Overlap ≥1.5x belt width
- Temperature control: 1.5-2.0MPa pressure at 145±5℃
- Quality inspection: X-ray NDT ensures ≥90% joint strength retention
Preventive Maintenance
- Lubrication: Auto-greasing every 500-1500h
- Idler replacement: Lifecycle database enables predictive maintenance
- Belt maintenance: Quarterly damage scans create digital twin models
Technical Selection Guide
Q = 3600Svρk
- Q - Capacity (t/h)
- S - Material cross-section (m²)
- v - Belt speed (m/s)
- ρ - Bulk density (t/m³)
- k - Slope coefficient (reference tables)
Power Calculation
P = (CgLv + QgH)/367η
- P - Motor power (kW)
- C - Friction coefficient
- L - Conveyor length (m)
- H - Lift height (m)
- η - Transmission efficiency
Quality Assurance
- Standards compliance: ISO 5048, DIN 22101
- Testing protocol: 72-hour loaded trial operation
- Warranty: 3-year coverage for core components
- Support: 48-hour global technical response