Длиннобазный ленточный конвейер представляет собой интеллектуальное транспортировочное оборудование, разработанное для работы на сложном рельефе и обеспечения протяженных маршрутов перевозки. В основе конструкции лежит модульный принцип проектирования, позволяющий достигать длины одной секции до 20 километров с минимальным радиусом горизонтального поворота 300 метров. Система объединяет технологии адаптации к рельефу местности, динамической компенсации натяжения и интеллектуального мониторинга, что позволяет заменить традиционные многоступенчатые схемы транспортировки и обеспечить непрерывную перевозку сыпучих материалов (руды, угля, песка и других) по любой местности.
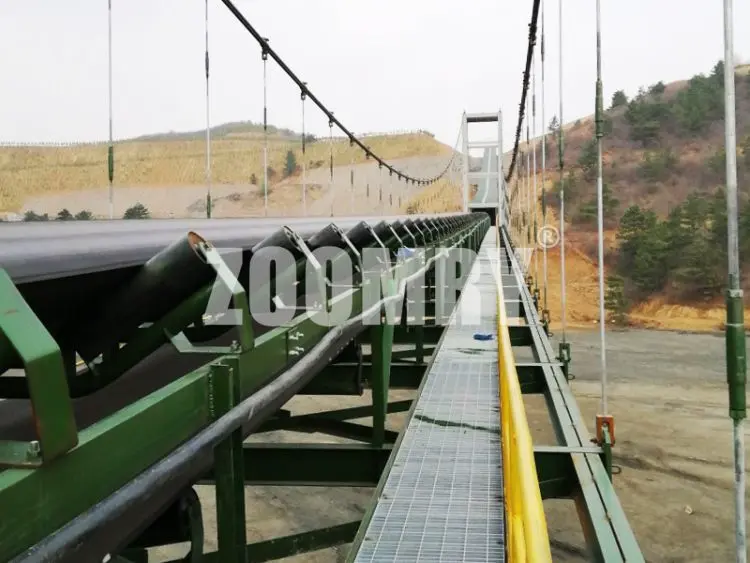
Основные технические параметры
Категория | Диапазон параметров | Технические характеристики |
---|
Базовые параметры |
|
|
Рабочая ширина ленты | 800-2600 мм | Индивидуальный подбор под характеристики материала |
Длина одной секции | 500 м - 15 км | Конструкция, адаптированная к рельефу |
Диапазон скоростей ленты | 0.8-4.0 м/с | Плавное регулирование скорости с помощью частотного преобразователя |
Параметры производительности |
|
|
Максимальная производительность | 12,000 т/ч | Угол наклона желобчатых роликов 35°-45° |
Максимальный размер куска | ≤350 мм | Встроенная система дробления крупных кусков |
Адаптация к рельефу |
|
|
Продольный уклон | -25°~+28° | Специальная противоскользящая конструкция глубокого желоба |
Радиус горизонтального поворота | ≥300 м | Система динамической коррекции положения ленты |
Характеристики компонентов |
|
|
Диаметр приводного барабана | Φ630-1800 мм | Толщина резиновой обкладки 15-25 мм |
Расстояние между амортизирующими роликами | 0.3-1.2 м | Конструкция с эластичными опорами для гашения вибраций |
Ключевые преимущества системы
Универсальность применения на любом рельефе
- Трехмерное планирование трассы: Длиннобазный ленточный конвейер использует ГИС-технологии моделирования рельефа для оптимального обхода природных и искусственных препятствий (здания, водные преграды), что минимизирует объем землеотводов
- Динамическая система изменения направления: Гидравлические поворотные механизмы обеспечивают минимальный радиус поворота 300 метров
- Технология компенсации уклона: Способность преодолевать подъемы до 28°, что особенно важно для работы в горнодобывающих районах со сложным рельефом
Система интеллектуального технического обслуживания (опционально)
- Комплексный мониторинг в реальном времени: Встроенные датчики 5 типов непрерывно отслеживают 12 критических параметров, включая натяжение ленты, боковое смещение, температуру узлов и другие
- Прогнозирующее обслуживание: Система анализа больших данных прогнозирует остаточный ресурс подшипников и других компонентов с заблаговременным предупреждением за 3 месяца до потенциального отказа
- Централизованное управление: Полная совместимость с системами SCADA для дистанционного контроля и управления всем конвейерным комплексом
Энергоэффективные и экологичные решения
- Технология прямого привода на постоянных магнитах: Коэффициент полезного действия достигает 96%, что обеспечивает снижение энергопотребления на 25% по сравнению с традиционными решениями
- Экологичная конвейерная лента: Применение специальной огнестойкой и антистатической ленты ST-2500 снижает уровень шума при работе до 75 дБ
- Альтернативные источники энергии: Опциональная возможность оснащения фотоэлектрическими панелями с системой накопления энергии, что позволяет экономить до 300,000 кВт·ч в год
Детализированный анализ конструкции
Приводной модуль
- Система дублированного привода: Обеспечивает сохранение 70% производительности при отказе одного из приводов
- Комбинированная система управления: Совместная работа гидромуфты и частотного преобразователя гарантирует плавный пуск и остановку оборудования
- Двигатели с постоянными магнитами: Степень защиты IP65 позволяет эксплуатировать оборудование в диапазоне температур от -30℃ до +50℃
Несущая конструкция
- Модульная система ферм: Стандартные секции длиной 12 метров с точностью монтажа до 5 миллиметров
- Защита от ветровых нагрузок: Конструкция рассчитана на устойчивость при ветровом давлении до 0.6 кН/м² (соответствует 10 баллам по шкале Бофорта)
- Антикоррозийная защита: Технология горячего цинкования обеспечивает срок службы не менее 25 лет даже в агрессивных средах
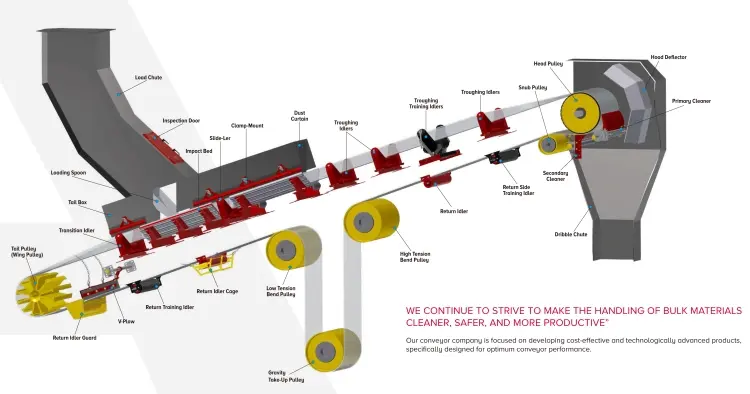
Системы интеллектуальной защиты
Тип устройства | Функциональные возможности | Стандарты установки |
---|
Двунаправленный датчик смещения | Трехуровневая система оповещения с автоматической коррекцией при отклонении на 5° | Устанавливается через каждые 30 метров |
Система обнаружения продольных разрывов | Матрица датчиков выявляет повреждения ленты от 20 мм | Монтируется в критических точках перегрузки |
Инфракрасные температурные датчики | Непрерывный контроль температуры барабанов с сигнализацией при достижении 70℃ | Устанавливаются на приводных и отклоняющих барабанах |
Типовые сферы применения
Транспортировка горной массы
Длиннобазный ленточный конвейер обеспечивает непрерывную перевозку руды от карьера к обогатительной фабрике или складу, преодолевая сложный горный рельеф. Конструкция оснащена роликоопорами с увеличенным углом наклона для работы на уклонах до 28°, а также специальными амортизирующими роликами, способными выдерживать нагрузку от кусков породы размером до 350 мм. В зонах значительных перепадов высот установлены системы рекуперации энергии, преобразующие энергию торможения в электрическую, что обеспечивает общую экономию энергии 18-25%.
Перевалка насыпных грузов в портах
Оборудование полностью соответствует требованиям перевалки массовых грузов в морских портах, обеспечивая взаимодействие между судном и береговыми складами. Герметичная конструкция загрузочных желобов в сочетании с системой тонкого водяного распыления поддерживает концентрацию пыли на уровне не более 5 мг/м³. Все металлоконструкции проходят двухступенчатую антикоррозийную обработку (горячее цинкование с последующим нанесением эпоксидного покрытия), гарантируя срок службы не менее 15 лет в условиях морской среды. Обеспечивается полная синхронизация с автоматизированными системами погрузки судов производительностью до 6000 тонн в час.
Перевозка нерудных строительных материалов
Специализированное решение для транспортировки песка, щебня и других строительных материалов от карьеров к бетонным узлам и строительным площадкам. Система оснащена специальным распределителем материала, предотвращающим расслоение фракций при перевозке. Критические участки оборудованы двухслойными укрытиями с системой аспирации, что обеспечивает уровень шума не выше 75 дБ(А) и минимальное пылеобразование. Для перевозки мелкодисперсных материалов используются специальные ролики с антиадгезионным покрытием, значительно снижающие налипание материала.
Топливоснабжение тепловых электростанций
Комплексное решение для транспортировки угля от разгрузочных устройств к складам и котельным отделениям ТЭС. В систему интегрированы металлодетекторы, магнитные сепараторы и другие защитные устройства. Применяется специальная огнестойкая и антистатическая конвейерная лента. Для регионов с холодным климатом предлагается опция подогрева с помощью электрических нагревательных элементов, предотвращающая обледенение внутри галерей. Обеспечивается интеграция с цифровыми системами управления топливным хозяйством для оперативного контроля теплотворной способности и оптимизации смешения углей.
Транспортировка сырья для цементной промышленности
Оптимальное решение для перевозки известняка от карьеров к цементным заводам с максимальной длиной одной секции до 12 километров. Конструкция включает специальные устройства для предотвращения пылеобразования в местах перегрузки и многоступенчатые пересыпные устройства с герметизацией в зонах значительных перепадов высот. Для работы с высокоабразивными материалами используются барабаны с керамическим покрытием, срок службы которых в 3 раза превышает стандартные решения. Обеспечивается полная интеграция с распределенными системами управления (DCS) для автоматизации всего процесса транспортировки.
Сравнительный анализ по сферам применения
Сфера применения | Адаптация к рельефу | Экологические требования | Приоритеты обслуживания | Требования к автоматизации |
---|
Горнодобывающая промышленность | Сложный горный рельеф (категория A) | Средний уровень | Ударопрочные элементы конструкции | Системы адаптации к рельефу |
Портовые терминалы | Ровная поверхность (категория B) | Строгие нормативы | Антикоррозийная защита | Интеграция с автоматикой погрузки |
Производство строительных материалов | Пересеченная местность (категория B+) | Повышенные требования | Герметичность системы | Точность дозирования |
Тепловая энергетика | Стационарные галереи (категория C) | Стандартные требования | Безопасность эксплуатации | Взаимодействие с системами ТЭС |
Цементная промышленность | Смешанный рельеф (категория A-) | Повышенные требования | Износостойкие компоненты | Оптимизация технологических процессов |
Монтаж и техническое обслуживание
Технология соединения лент на месте эксплуатации
- Совмещение концов ленты: Применение лазерного центровщика обеспечивает точность совмещения до 2 миллиметров
- Подготовка соединения: Ступенчатая зачистка поверхности с обеспечением длины нахлеста не менее 1.5 ширины ленты
- Контроль процесса вулканизации: Поддержание давления 1.5-2.0 МПа при температуре 145±5℃
- Контроль качества: Проведение рентгенографического контроля неразрушающим методом с обеспечением прочности соединения не менее 90% от исходного материала
Стратегия профилактического обслуживания
- Система централизованной смазки: Автоматическая подача смазочных материалов с регулируемым интервалом 500-1500 часов работы
- Управление ресурсом роликов: Ведение базы данных по наработке и прогнозирование сроков замены
- Мониторинг состояния ленты: Квартальное сканирование поверхности с созданием цифровой модели износа
Методика подбора оборудования
Формула расчета требуемой ширины ленты
Q = 3600Svρk
- Q - Производительность конвейера (тонн/час)
- S - Площадь поперечного сечения материала (м²)
- v - Скорость движения ленты (м/с)
- ρ - Насыпная плотность материала (тонн/м³)
- k - Поправочный коэффициент, учитывающий угол наклона (определяется по таблицам)
Методика расчета мощности привода
P = (CgLv + QgH)/367η
- P - Требуемая мощность двигателя (кВт)
- C - Коэффициент сопротивления движению
- L - Длина конвейера (метры)
- H - Высота подъема материала (метры)
- η - Общий коэффициент полезного действия привода
Система гарантийных обязательств
- Соответствие международным стандартам: ISO 5048, DIN 22101
- Программа испытаний: 72-часовые испытания под рабочей нагрузкой
- Гарантийные сроки: 3 года на основные узлы и компоненты
- Техническая поддержка: Глобальная служба реагирования в течение 48 часов